Reducción del biorreactor al formato microfluídico
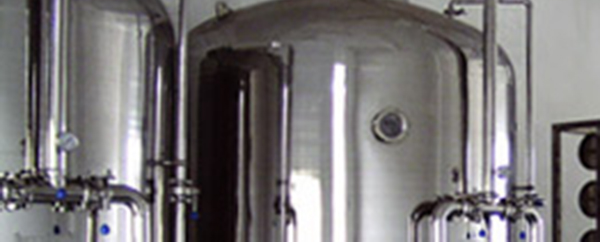
El motivo general para reducir los biorreactores es usarlos para la optimización del proceso. Debido a su pequeño tamaño, reducen el costo, aumentan el rendimiento y reducen la mano de obra involucrada. Además, los tiempos de reacción y proceso son más cortos debido a tiempos de difusión más cortos de factores solubles. Otro factor determinante es que con dispositivos más pequeños es más fácil optimizar procesos en paralelo y que los dispositivos microfluídicos se presten para ser automatizados. Sin embargo, no están al mismo nivel de automatización que los sistemas robóticos de manejo de líquidos. Hay ejemplos reales donde los microrreactores funcionan mejor que los sistemas convencionales. Un ejemplo es la eficiencia de la digestión de la enzima inmovilizada en las paredes de un microtubo, que tuvo un mayor rendimiento en comparación con los sistemas de digestión en solución. Esto se debe a que los microfluídicos tienen una relación superficie / volumen mucho mayor que los recipientes del reactor.
Muchos de los reactores descritos en este capítulo se han comparado con reactores a escala de banco que muestran resultados similares. La cuestión de si el microbioreactor puede ampliarse a biorreactores de tamaño industrial permanece.
Métodos de microfabricación para biorreactores en un chip
Hay varias formas de fabricar un microsistema. Uno de estos procesos es la litografía suave, una técnica que es uno de los métodos más utilizados para la fabricación de microfluidos. Además, la técnica de fabricación mecánica fina es una opción, ya que los agujeros pueden perforarse hasta 100 μm de diámetro. En estos días, el mecanizado con láser es más accesible, pero para alcanzar una alta precisión se necesita un láser de alta precisión, lo que elevará el precio.
Para realizar la microfabricación, en la mayoría de los casos, se necesita una sala limpia para evitar que el polvo se deposite en el dispositivo. Dependiendo del método de fabricación utilizado, se necesita una clase diferente de sala limpia. Clase, en este caso, significa el número de partículas de polvo por metro cúbico. Para hacerse una idea, para la litografía suave se necesita una limpieza de 1000–10000partículas − 3 (ISO clase 4-5). En el otro lado de la escala está la fabricación de microelectrónica, de 1 a 10 partículas m − 3(ISO clase 1 – 2), al definir un tamaño de partícula de 0.3 μm.
Grabado de silicio / vidrio
Aunque el vidrio podría ser el material más deseado para usar en aplicaciones de biotecnología debido a sus propiedades ópticas y compatibilidad biológica, es un material difícil de procesar debido a su fragilidad. Existen algunos métodos para procesar el vidrio: granallado en polvo, grabado profundo con iones reactivos (DRIE), grabado húmedo y mecanizado con láser. De todos estos métodos, el grabado húmedo con HF da buenos resultados, a pesar de que es un proceso isotrópico, pero es el más peligroso de los métodos, que no se recomienda para un laboratorio estándar, ya que son necesarias normas especiales de capacitación y seguridad. Además, no todos los laboratorios permiten HF en sus instalaciones. DRIE es un método de grabado muy lento, y el equipo es muy costoso, lo que no siempre está disponible en salas limpias. Sin embargo, el proceso puede ser extremadamente preciso para características pequeñas (0.5 μm). La voladura de polvo también dará resultados significativos, excepto que las paredes se ahusan en un ángulo de aproximadamente 12-15∘, pero el tamaño mínimo de la característica es de alrededor de 50 μm.
Litografía suave
Desde la introducción de la litografía suave ha provocado el despegue de la microfluídica. Es un método de moldeo de réplica relativamente barato con una alta rotación posible. Sin embargo, la obtención de un molde requeriría el uso de una sala limpia equipada con litografía, que es básicamente un alineador de máscara (u otra fuente de luz UV; [42]), un recubrimiento por rotación, placas calientes y un banco de solventes. La fotorresistencia más utilizada es SU8, que está disponible en diferentes viscosidades, lo que da como resultado diferentes alturas de características. Dependiendo del tamaño de la función, hay diferentes opciones de máscara. Para todo lo que supere los 20 μm, se pueden imprimir máscaras de aluminio. Para características entre 5 y 20 μm, se necesitan máscaras de soda-lima (∼ $ 500–1000, dependiendo de la cantidad de características en el). Para características entre 0.5 y 5 μm, se necesitan máscaras de cuarzo (> $ 1500). Para tamaños de características más pequeños, el proceso se vuelve un poco más complicado al usar un paso a paso, que básicamente reduce los tamaños de características en la máscara al transferir ópticamente el patrón a través de una lente.
Estampado en caliente
Para ampliar la producción, se podría considerar la impresión. Este método utiliza plásticos, como PMMA (o acrílico) para hacer chips en grandes cantidades mediante el uso de un molde de silicio o metal para presionar bajo presión en plástico calentado. Los tamaños de características en el rango submicrónico se pueden replicar. Este método solo es recomendable para la producción a gran escala, no para procesos de desarrollo rápido.